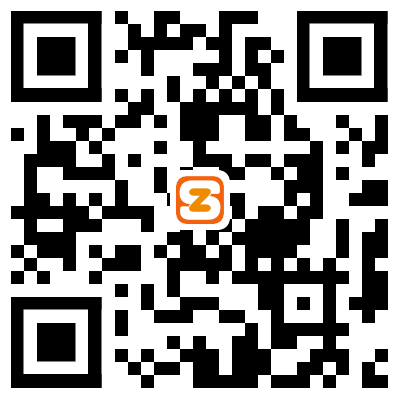

濟南法特數(shù)控機械有限責任公司
主營產(chǎn)品: 磨床
雙軸鉆銑床定做-龍門移動式鉆銑床定做-龍門移動式鉆銑床
價格
訂貨量(臺)
¥200000.00
≥1
店鋪主推品 熱銷潛力款
䀋䀐䀋䀔䀐䀋䀑䀌䀎䀐䀍





濟南法特數(shù)控機械有限責任公司是數(shù)控角鋼線、聯(lián)接板沖孔機、管板高速鉆、龍門鉆、角鋼鉆、法蘭鉆等產(chǎn)品專業(yè)生產(chǎn)加工的私營有限責任公司,公司總部設在濟南市長清區(qū)平安北路,濟南法特數(shù)控機械有限責任公司擁有完整、科學的質量管理體系。濟南法特數(shù)控機械有限責任公司的誠信、實力和產(chǎn)品質量獲得業(yè)界的認可。歡迎各界朋友蒞臨濟南法特數(shù)控機械有限責任公司參觀、指導和業(yè)務洽談。
數(shù)控平面鉆不銹鋼鉆孔時應注意哪些問題
在不銹鋼工件上鉆孔常采用麻花鉆,對淬硬不銹鋼,可用硬質合金鉆頭,有條件時可用超硬高速鋼或超細晶粒硬質合金鉆頭。鉆孔時扭矩和軸向力大,切屑易粘結、不易折斷且排屑困難,加工硬化加劇,鉆頭轉角處易磨損,鉆頭剛性差易產(chǎn)生振動。因此要求鉆頭磨出分屑槽,修磨橫刃以減小軸向力,修磨成雙頂角以改善散熱條件。
鉆削不銹鋼時,經(jīng)常發(fā)現(xiàn)鉆頭容易磨損、折斷,孔表面粗糙,有時出現(xiàn)深溝而無法消除;孔徑過大,孔形不圓或向一邊傾斜等現(xiàn)象。在操作時應注意下列事項:
幾何形狀必須刃磨正確,兩切削刃要保持對稱。鉆頭后角過大,會產(chǎn)生“扎刀”現(xiàn)象,引起顫振,使鉆出的孔呈多角形。應修磨橫刃,以減小鉆孔軸向力。
鉆頭必須裝正,保持鉆頭鋒利,用鈍后應及時修磨。
合理選擇鉆頭幾何參數(shù)和鉆削用量,按鉆孔深度要求,應盡量縮短鉆頭長度、加大鉆心厚度以增加剛性。使用高速鋼鉆頭時,切削速度不可過高,以防燒壞刀刃。進給量不宜過大,以防鉆頭磨損加劇或使孔鉆偏,在切入和切出時進給量應適當調小。
充分冷卻潤滑,切削液一般以硫化油為宜,流量不得少于5~8L/min,不可中途停止冷卻,在直徑較大時,應盡可能采用內冷卻方式。
認真注意鉆削過程,應及時觀察切屑排出狀況,若發(fā)現(xiàn)切屑雜亂卷繞立即退刀檢查,以防止切屑堵塞。還應注意機床運轉聲音,發(fā)現(xiàn)異常應及時退刀,不能讓鉆頭在鉆削表面上停留,以防鉆削表面硬化加劇。


濟南法特數(shù)控機械有限責任公司是數(shù)控平面鉆、數(shù)控角鋼線、聯(lián)接板沖孔機、管板高速鉆、龍門鉆、角鋼鉆、法蘭鉆等產(chǎn)品專業(yè)生產(chǎn)加工的私營有限責任公司,歡迎各界朋友蒞臨濟南法特數(shù)控機械有限責任公司參觀、指導和業(yè)務洽談。
據(jù)生產(chǎn)需要,數(shù)控鉆床的工作臺需要進行相應的設計。目前其工作臺主要分為回轉工作臺和分度工作臺,這兩種工作臺是有著不同的功能的,回轉工作臺的功能包含分度工作臺的,所以工作臺設計為回轉的。在對數(shù)控鉆床工作臺設計上,選取滾珠絲杠螺母機構時候,還需對絲杠的導程進行計算。
事實上,滾珠絲杠螺母機構對于數(shù)控鉆床工作臺的使用有著重要的作用,可以增強工作臺的平穩(wěn)性。而且它能保證工作臺在加工時候的高精度,高可靠性,同時滾動絲杠螺母機構的壽命比較長,降低對數(shù)控機床元件的更換頻率,耐用性特別強,對于主軸和工作臺之間的聯(lián)系和反饋同步性起到了關鍵的作用。
而滾動絲杠螺母機構的內部主要是由螺桿、螺母、滾珠組成,螺母固定在工作臺上,滾珠鑲嵌在螺母和絲杠中,使螺母能沿著絲杠旋轉做運動。該機構可以將電動機的旋轉運動轉化為工作臺的直線運動。而數(shù)控鉆床的工作臺設計上,電動機是它的一個重要部件,是工作臺的動力元件,選取交流伺服電機作為工作臺的動力裝置,這種電動機的速度低,但轉矩大,對工作臺及工作臺上的零件都可以使其運動。
對于數(shù)控鉆床而言,其工作臺上的軸承在進行安裝的時候,需要軸承座,軸承座是將內圓與軸承的外圓配合,同時軸承座的端面還要對軸承定位的作用。
總的來說,在加工一些高精密零件的時候,使用數(shù)控鉆床很有必要。該設備對整個孔的精度是一個保證,同時設計師還要不斷地對數(shù)控鉆床機構進行性能提升,使其性能更優(yōu)良,加工更效率,不斷更新工藝。
數(shù)控平面鉆如果選用的是普通碳素鋼的鉆頭不合適,不銹鋼由于塑性變形大,熱強度高,加工中容易加工硬化現(xiàn)象,增大了切削抗力和刀具磨損,切屑的卷曲折斷也比較困難。因此加工不銹鋼比較困難。
合理選擇刀具材料是保證高效率切削加工不銹鋼的重要條件。根據(jù)不銹鋼的切削特點,要求鉆不銹鋼鉆頭材料應具有耐熱性好、耐磨性高、與不銹鋼的親和作用小等特點。目前常用的刀具材料有超硬高速鋼,粉末冶金高速鋼和硬質合金三種。
